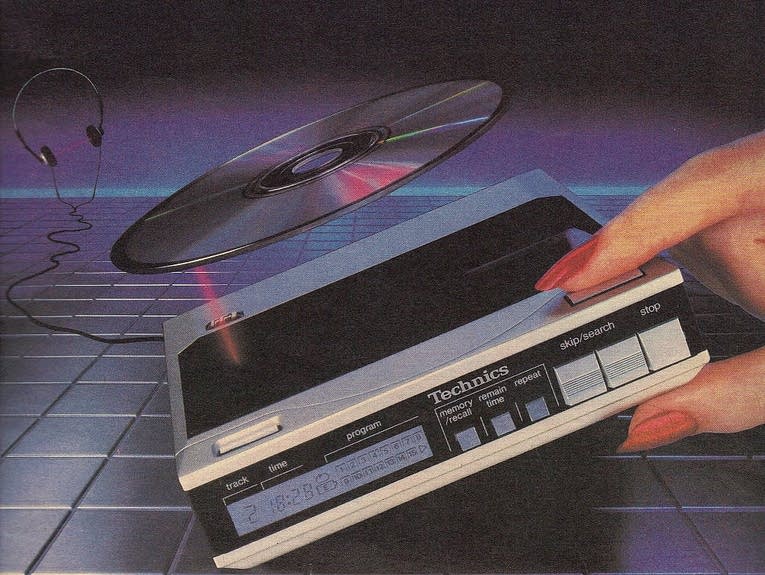

Now as we have said about routing tracks, we have to understand that this track placing or routes and via have rules that is the manufacture can only make them physically in a certain way we cannot draw and demand something which is lets say very small and very close placing of copper tracks or components as you have to understand there are physical machines, etching solutions, copper depositors which will work at some point of time on your designed PCB and they have some very real physical and practical limitations which are inevitable.
So, we cannot place copper tracks too close, we cannot place components too close, we cannot make via too close or close to a drill point. We cannot drill too close and so on. Also due to this there are auto routers which help in taking this DRC in account and the software or the algorithm or the computer as we see can just place or draw the tracks all by itself and there is just no need to worry about breaking rules and creating huge trouble.
So in this way our PCB design gets completed. I know this is not a very detailed explanation but it is something or the series is something that can at least give you a rough idea about what is happening.
So for now we have only discussed about how the two layers are, but depending on the use case, there can be more than two layers and in that case the manufacturers have more copper sand witches sand witched and through our given GERBER information, what diagrams are to drawn on sides are conveyed and all are drawn independently and then sand witched.
Now I have said there are files which convey information, so
I have a point to add that these all assembly are done in parts and only the
diagram part and drill parts are done with the help of drill machines and photo
developers and oxidation and copper deposits etc.
Now as we sort of now know how the PCB is manufactured lets
start where we left off, that is after logical diagram and attaching
footprints.
So, after all those we just have to draw circuits and those
are just how copper tracks will go where the components will be placed, where
the power lines will be where the ground planes will be and so on. Also first
we just have to place components in place as we want and they are connected
with the help of raster nets which are derived from the logical diagram
actually, and these raster nets are then to be made copper tracks that is how
physically copper will run from one component to another and how the ground
planes would be. These running of copper tracks is called routing and has some
specific rules.
So, after we have done logical schematic diagram with footprints attached we can now just start drawing on the PCB using our softwares Physical layout editor or a board designer, here what we draw initially is on the top surface of the PCB.
Ok so as I have said surface and we are into physical view
now so lets describe how physically the PCB is prepared in the real world in
fabrication centre. So, in fabrication centre they start with something called
a copper sandwich, which is copper layers on either side with a dielectric
material between them, the dielectric material is what the whole PCB gets
support on and the top and bottom sides are copper so all the electrical
diagrams and contacts and contact pads and via are done on them using first
marking with help of UV and then etching.
So, first the raw material as described is taken and then
the diagrams from the customer are taken and transferred on the copper layers
as per given formats. Now for this transfer there is no specific PCB design
file, but as we might have heard of we have something called as GERBER files
which are files which are generated from the PCB design software and have all
the information about how the board drawings would be and how the silkscreen
that is all the writings and diagrams would be and how the copper pads will be
exposed after the solder mask and a NCDRILL file which tells where the
mechanical boundaries are and how the holes are to be drilled.
These footprints I am talking of are provided by
manufacturers itself and some by PCB manufacturers also, and after we make
logical diagrams we have to attach them or in some softwares they are
automatically attached for general non-conflicting components. The footprints are the white coloured markings
we see for most PCBs, which is just below the components are placed.
In some cases we might have to attach special parts like a
heat sink or a some display whose exterior part is not given in footprint in
that case we can manually add a symbol also or do it during physical design
process.
![]() |
Main SoC of a Featured Phone(ikal) |
All the Photograph Posts are original and belongs to this blog, Do not use them without credits or mentioning that they are from this blog or who shot the original picture.
A text-based blog which aims to explain engineering behind some popular electronics & communication devices in simple words. Also we try to provide tutorials and technical reviews about popular Software or about Electronic Design Automation(EDA) Software. . . . .Simple User Interface. More Text. More Explanation.